SkunkWorks
Well-Known Member
At the end of last season, during my last ride in the fall, I had noticed a bit of gear-oil had dripped onto the rear wheel.
You could see the telltale streaking on the tire from it spinning.
I had simply parked the bike in the Garage. I already had the output-seal on the shelf, so I figured I would get to it at some point.........
Fast-forward to this weekend.
I pulled the rear wheel to inspect and replace the output seal.
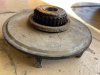
Cush-Drive Plate is dry....................Hmmmm, figured it would have some gear oil wetness on it.
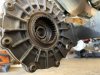
Does not appear that it was leaking from the output seal.
So I take a look underneath.
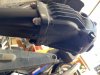
Seems like it was leaking out of the drain hole, and blowing back all over the swingarm and final-drive housing.
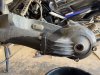
So I drained the fluid out, and removed the final-drive assembly from the swingarm.
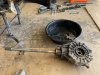
Sure enough!
Gear oil inside the Swingarm leaking from the input seal.......
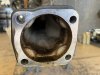
You could see the telltale streaking on the tire from it spinning.
I had simply parked the bike in the Garage. I already had the output-seal on the shelf, so I figured I would get to it at some point.........
Fast-forward to this weekend.
I pulled the rear wheel to inspect and replace the output seal.
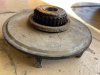
Cush-Drive Plate is dry....................Hmmmm, figured it would have some gear oil wetness on it.
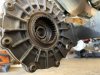
Does not appear that it was leaking from the output seal.
So I take a look underneath.
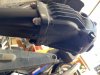
Seems like it was leaking out of the drain hole, and blowing back all over the swingarm and final-drive housing.
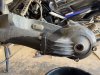
So I drained the fluid out, and removed the final-drive assembly from the swingarm.
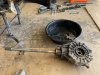
Sure enough!
Gear oil inside the Swingarm leaking from the input seal.......
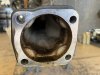